Notable Features |
|
IFCII |
 |
Steel structure with concrete core (hydraulic
climb from system) |
 |
Large composite mega-columns |
 |
Steel permanent formwork for slabs |
 |
Prefabricated staircases
(steel and concrete) |
 |
Hardiwall |
|
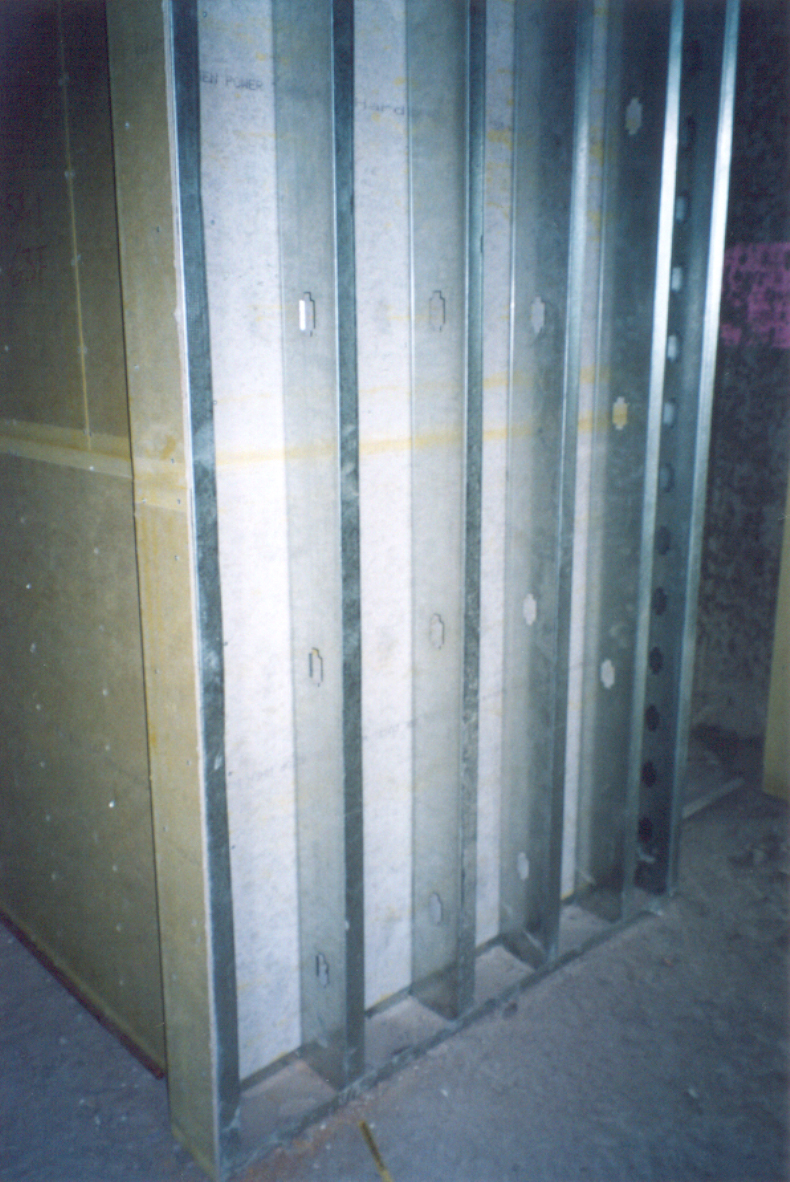 |
 |
Raised access floor system |
|
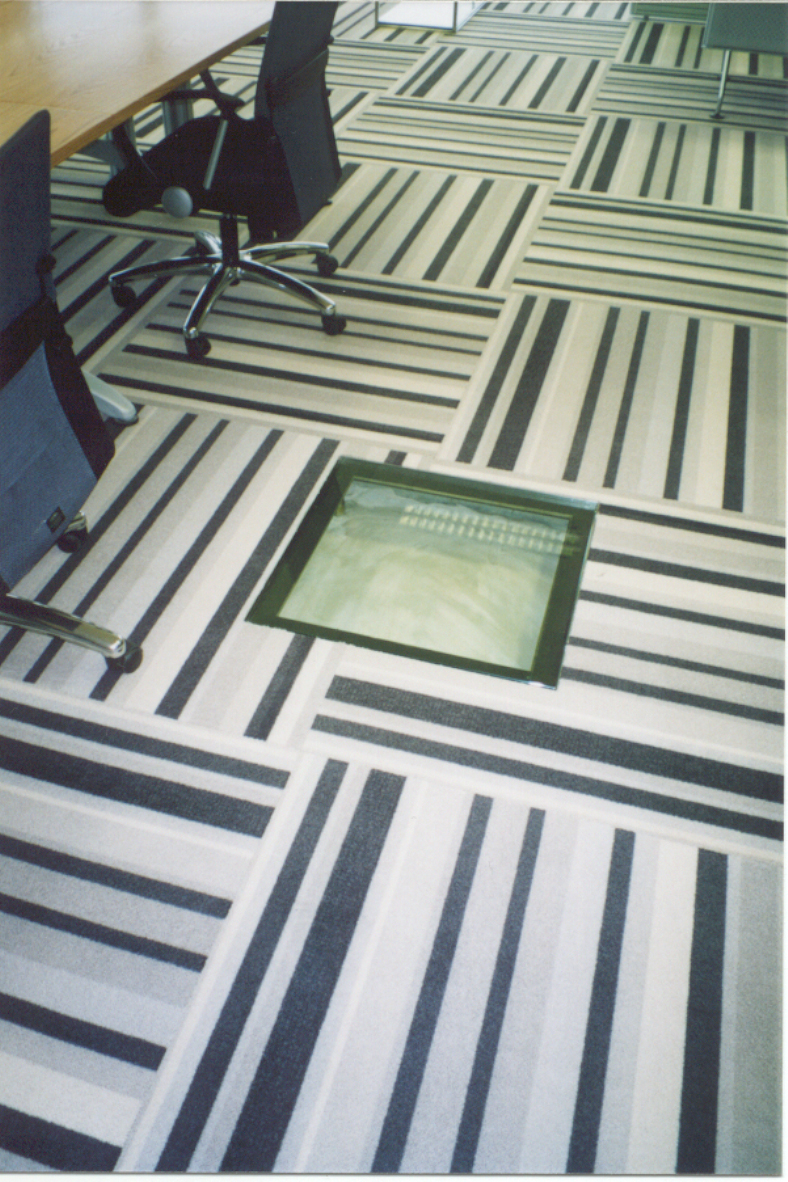 |
 |
Metal and bamboo scaffoldings
(inside works) |
|
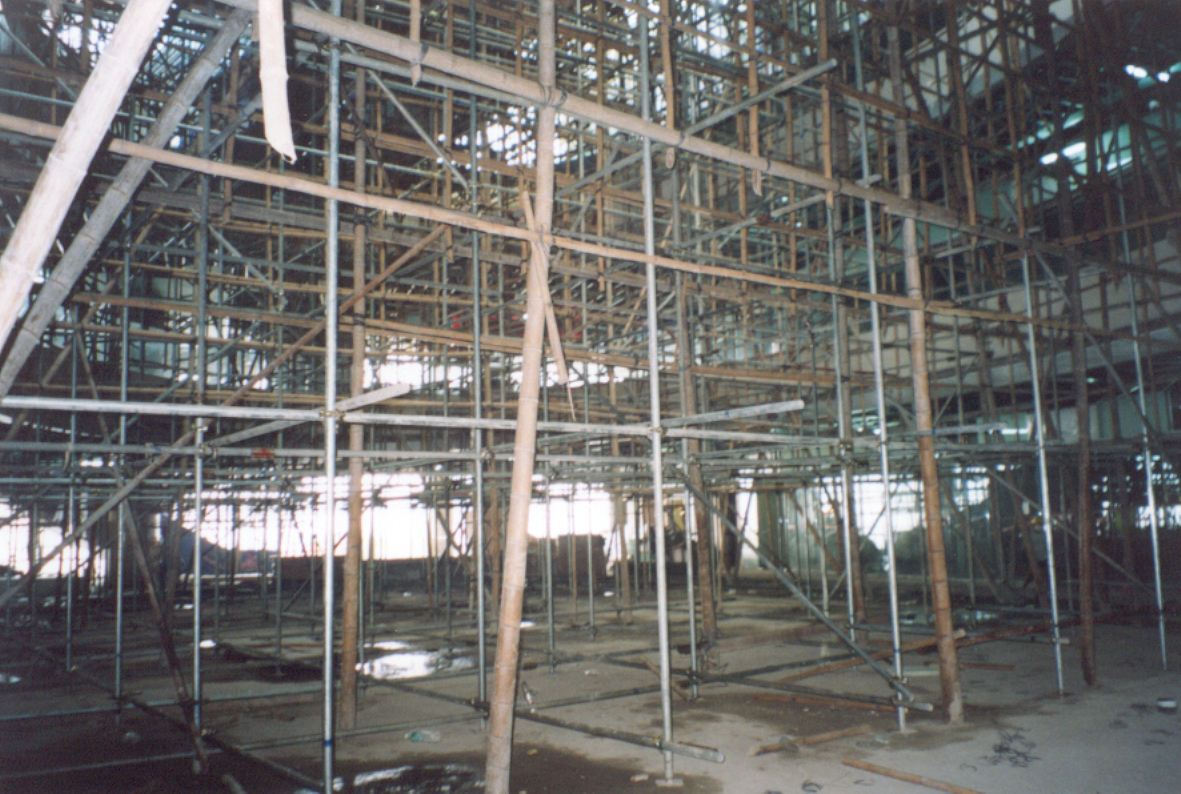 |
 |
Metal scaffolding (inside works) |
 |
Prefabricated curtain wall |
 |
On-site concrete batching plant |
 |
Diaphragm wall cofferdam |
 |
Top down construction technique
(for 6 level basement) |
 |
Steel prefabricated retail bridges |
 |
Muck Hoist |
 |
Basic Information |
Location
: |
Central, Hong Kong |
Building Type : |
Grade A commercial
building |
Contract
Period : |
The One IFC and
South IFC Mall were completed in December 1998,
The IFCII will be completed in mid-2003,
The North IFC Mall in late 2002,
The Hotel and Suite Hotel in 2004. |
Developers
: |
MTR Corporation Ltd.
(Grantee of site), IFC Development Ltd., Sun Hung Kai Properties Ltd.,
Henderson Land Development Co. Ltd., The Hong Kong and China Gas Co.
Ltd., Bank of China Group Investment Ltd. |
Architect : |
Cesar Pelli & Associates Inc., Rocco
Design Ltd. |
Project Manager
: |
Central Waterfront Property Project
Management Co. Ltd.
(jointly owned by : Sun Hung Kai Properties Co. Ltd.)
Henderson Land Development Co. Ltd.) |
Civil & Structural
Engineer
: |
Ove Arup & Partners |
E&M Engineer : |
J. Roger Preston
Ltd. (Northern Site), Meinhardt (M&E) Ltd. (Southern Site) |
Quantity Surveyor
: |
Levett & Bailey |
Structural Auditor : |
Leslie E. Robertson Associates (New
York) |
E&M Auditor
: |
Jaros, Baum & Bolles Consulting
Engineers (New York) |
Main Contractor
: |
E Man-Sanfield JV Construction Co. Ltd. |
Basement
Construction Manager
: |
Gammon Construction Ltd. |
Diaphragm Wall and
Foundations
: |
Aoki Corporation |
Retail Bridges
: |
Gammon Construction
Ltd. |
Structural Steel
for IFCII
: |
JV of NKK Corp. and
Sumitomo Corp. |
Curtaim Wall for IFCII
: |
Permasteelisa HK
Ltd. |
Lifts
: |
Otis Elevator Co.
(HK) Ltd. |
Escalators
: |
Schindler Lifts (HK) Ltd. |
Podium Curtain
Wall Consultant
: |
Arup Facade Engineering |
Office Tower
Interior Designer
: |
Hirsch Bedner Associates |
Landscape
Consultant
: |
Urbis International Ltd. |
 |
. |
Overview |
The IFC
complex located above the airport railway’s Hong Kong station comprises the
completed One IFC 38-storey tower, the IFCII 88-storey tower, a 640,000sqft
shopping mall and the Four Seasons Hotels. |
|
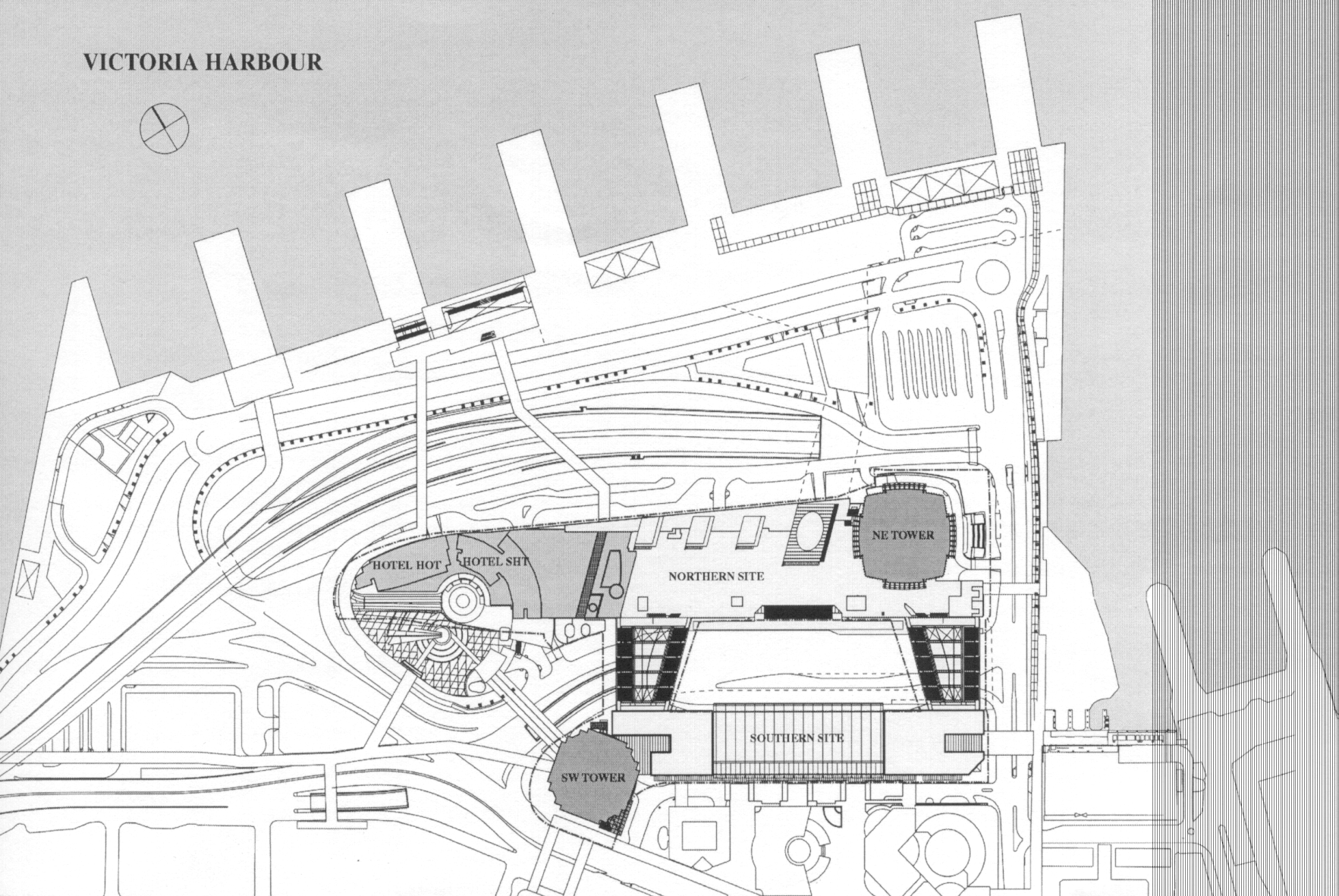 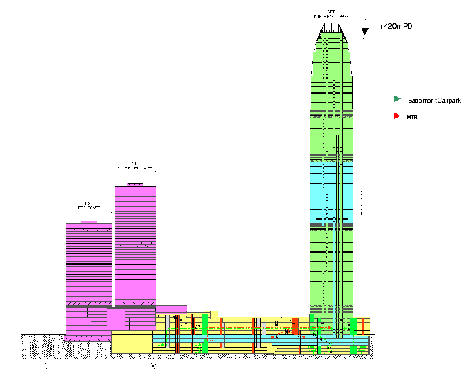 |
|
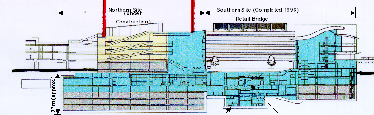 |
|
|
 |
One IFC : |
The 38-storey
One IFC building completed in December 1998, comprised 785,000sqft of office
space. This building received a Quality Award Building in 2002. |
|
 |
The Four Seasons Hotel and Suites : |
The Four
Seasons Hotel will comprise of approximately 400 guest rooms with facilities
including ballrooms, shops, banquet halls, conference rooms, swimming pools,
health spa and restaurants. The four Seasons Suites will comprise of about 600
guest units. |
|
 |
IFCII : |
The IFCII
88-storey building is the third tallest building in the world with a height of
420m. The structure is made of concrete core, steel outriggers at three levels
and large composite mega-columns. The tower was built with a 3 day-cycle floor
construction.
The traditional
construction techniques were not used (apart from complex details) mainly
because of the issues of vertical transportation of material supplies and waste
generation, as well as the issue of time. The cost for traditional foundation
would have cost about 130-150/sqft and for formworks (superstructure) about
150/m2, compared with a reduction of approximately 50% of the actual cost using
innovative techniques. |
|
|
On-site Facilities : |
 |
The huge
project used a central project office (CPO) on-site to improve coordination of
design and construction saving cost and time. |
 |
The
construction of a marine access at Pier 2 reduced traffic and environmental
impact. |
 |
The on-site
concrete batching plant reduced cost and transportation. |
|
 |
Diaphragm Wall Cofferdam |
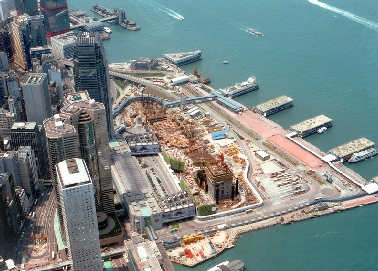 |
The
construction of a 61.5 m diameter, 38 m deep, 1.5 m thick diaphragm wall
cofferdam saved 9 months in North East Tower programme, and reduced cost. |
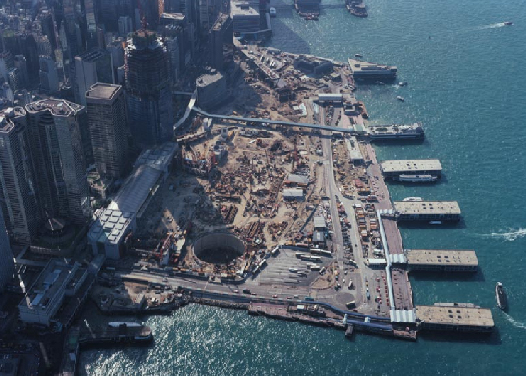 |
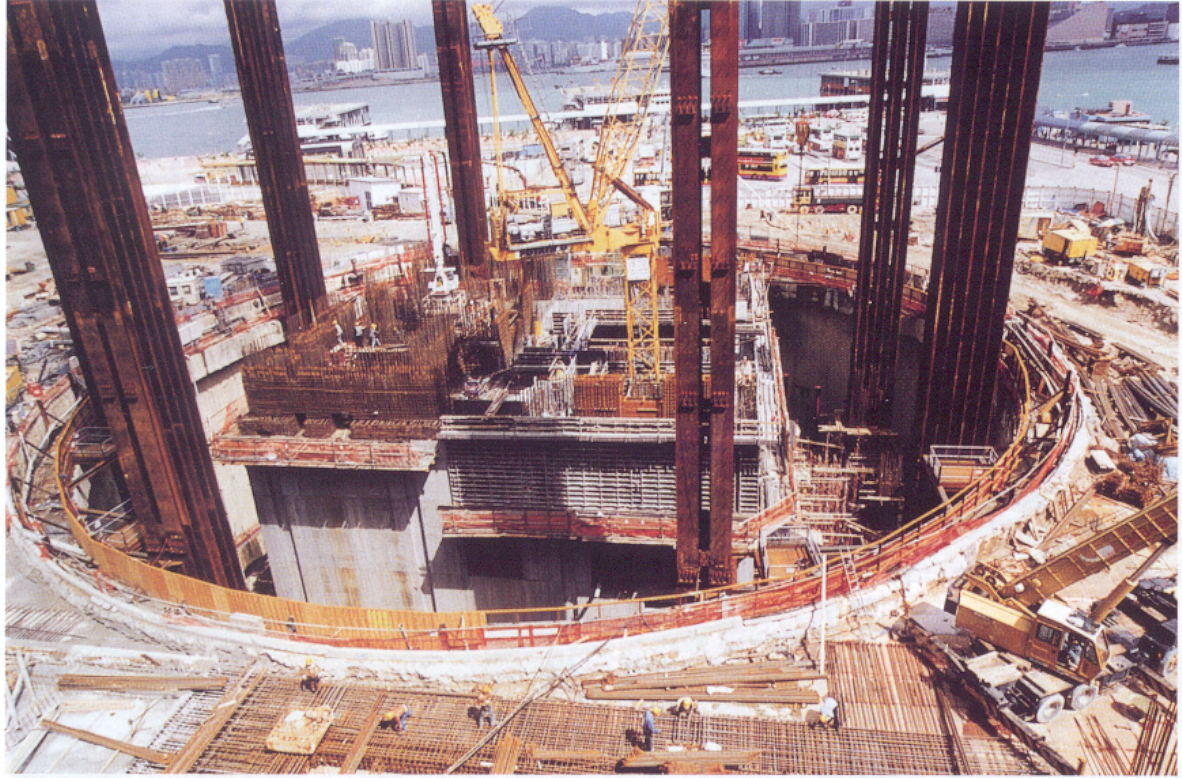 |
 |
|
Top Down Construction Technique |
It was used
for the 6 level basement minimizing movement of existing station. |
|
 |
|
Sources |
|
 |
Hong Kong
Station Development International Finance Centre Power Point
Presentation, Central Waterfront Property Project Management Co. Ltd. |
 |
China
Building Development, issue No.1, 2002. |
 |
Construction
& Contract News, 2001 No.4, p40-43. |
 |
Building
Journal Hong Kong China, April 2002, p60-61. |
 |
Building
Journal Hong Kong China, May 2001, p14. |
 |
www.skyscrapers.com |
 |
|
|
![]() |
|
Areas |
 |
Southern Site : 85,063 m2 |
One IFC : 72,880 m2 |
IFC mall : 12,183 m2 |
|
 |
Northern Site : 330,837 m2 |
IFC2 : 181,310 m2 |
Retail : 47,277 m2 |
Hotel : 102,250 m2 |
|
 |
Grand Total : 415,900 m2 |
 |
Public Open Space : 13,000 m2 |
 |
Development Carparks : 1,341 spaces |
 |
AEL Carparks : 450 spaces |
|
Concrete Core |
|
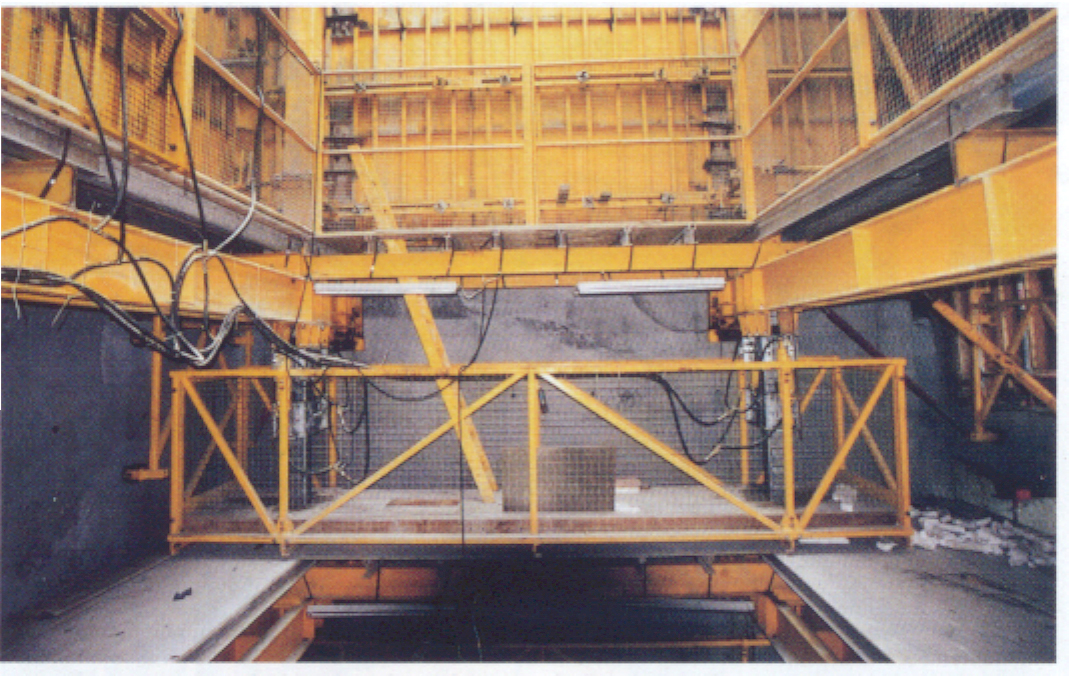 |
|
The concrete
core was built with hydraulic climbform system saving time and ensuring quality.
The same formwork was used for the whole concrete core reducing the generation
of construction waste on-site. Traditional techniques would have been difficult
considering the issue of vertical transportation of materials and wastes, as
well as time consuming. Due to the immense size of the wall sections, two sets
of climbform were used in staggered stages for casting the concrete core. Tie
members linked the two portions into a rigid central structure. At the lower
levels, the core wall is 1.5 m thick. |
|
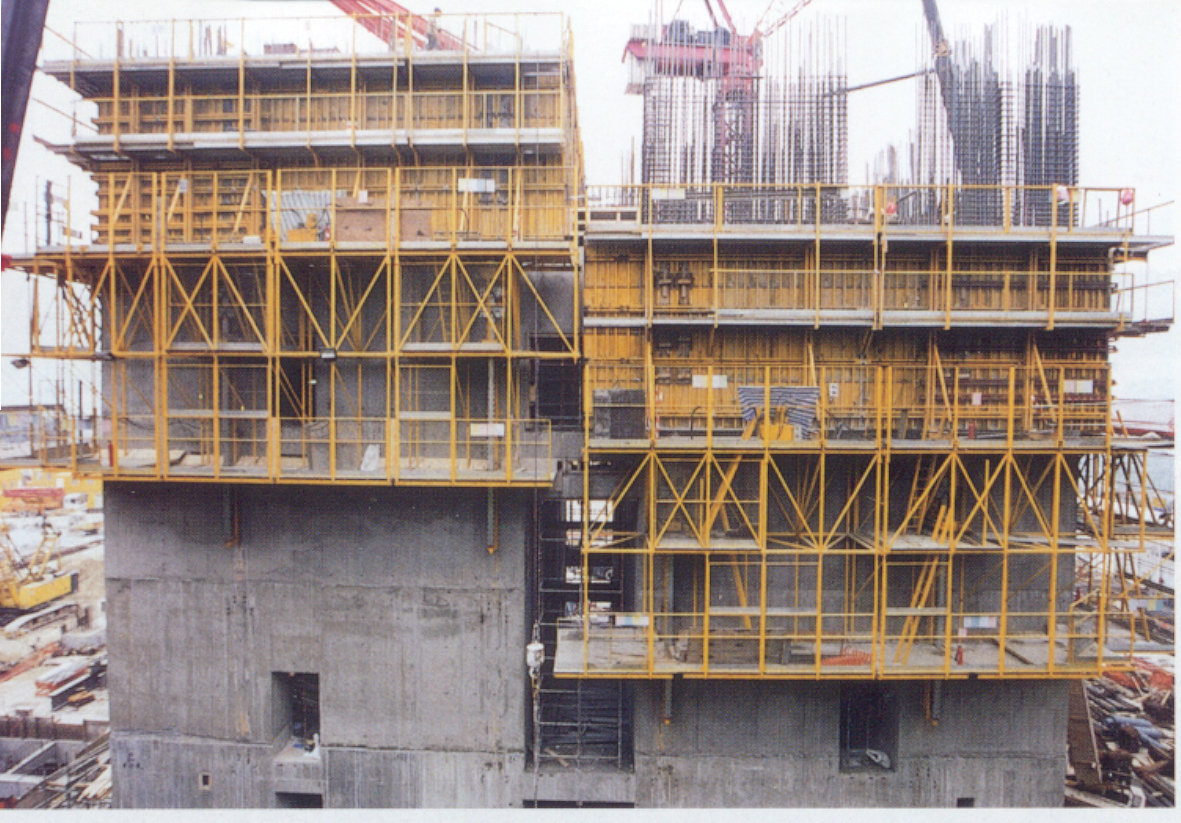 |
|
 |
Large Composite
Mega-columns |
|
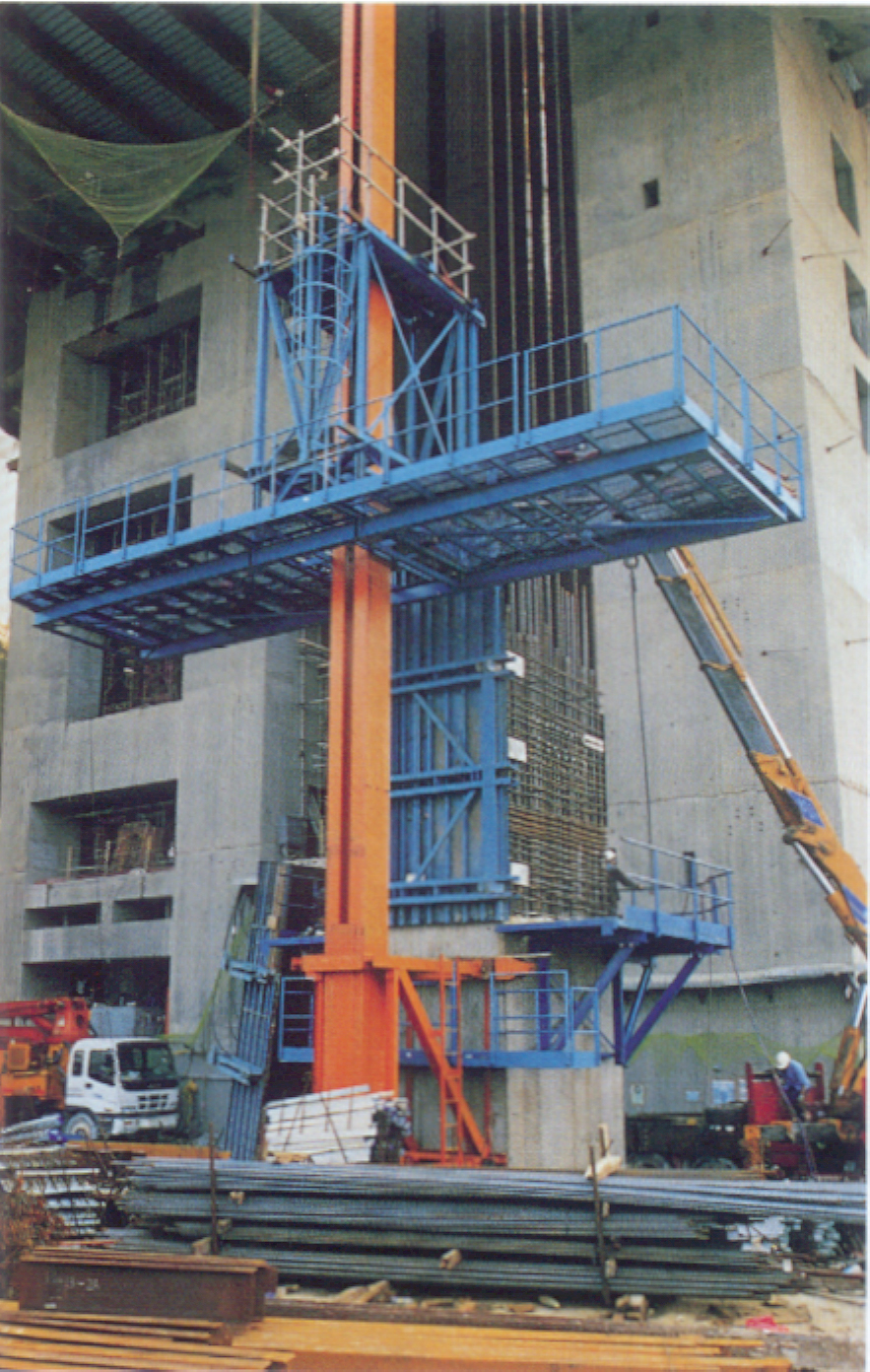 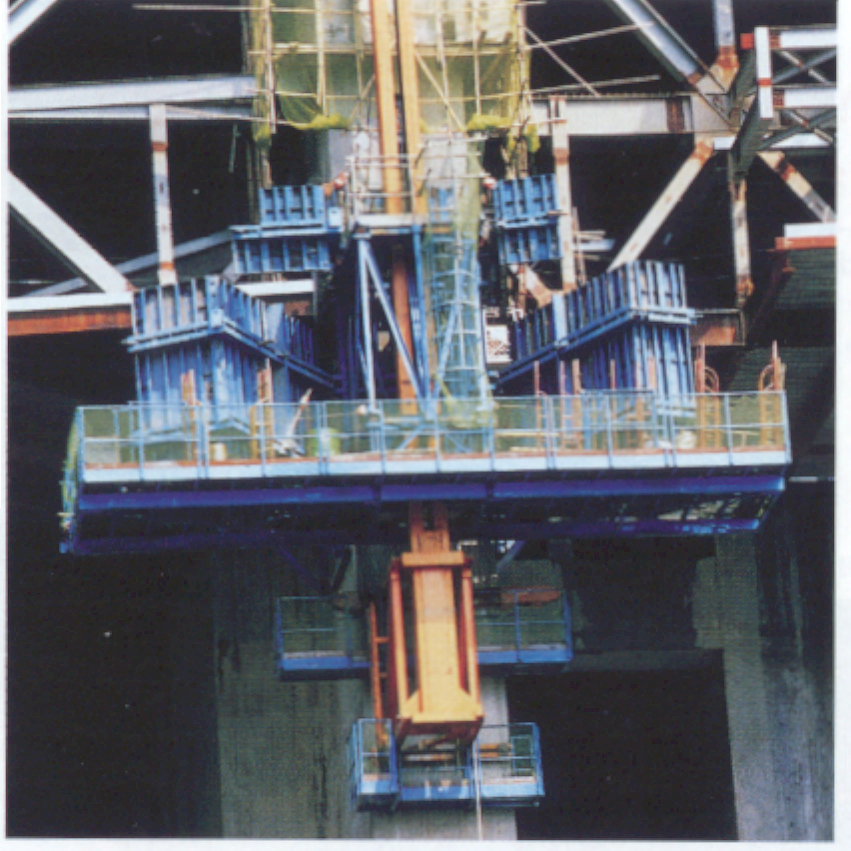 |
|
The steel and
concrete composite mega-columns were cast with a specially designed form system.
The form was mounted with anchor bolts on to the lower part of the column.
Hydraulic jacks inside the central post could lift the form when the concreting
of the lower parts was completed. |
|
Steel Permanent
Formwork for Slabs (Condek) |
|
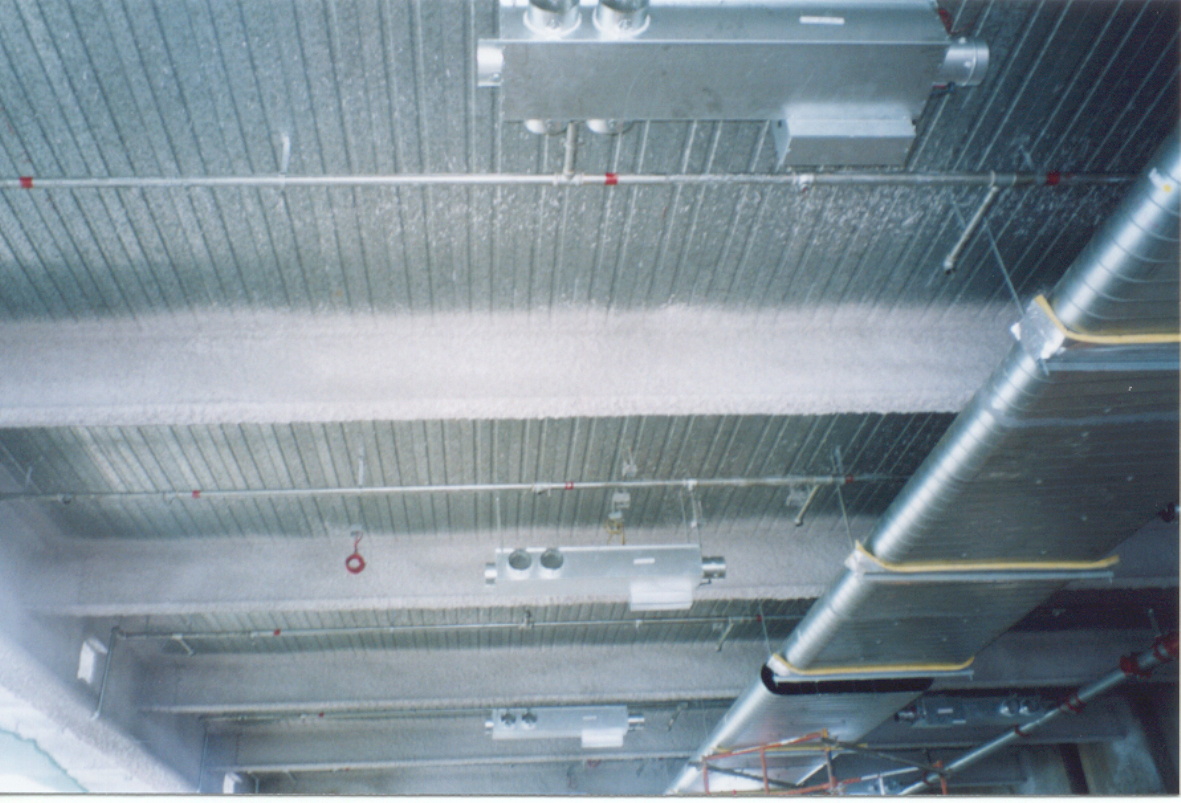 |
|
Steel
permanent formwork was used for the slabs saving time (hoisting and removing
time) and reducing on-site waste generation. Once the permanent formwork and the
reinforcement bars installed 1.25 mm thick concrete was poured (pumping system
and robotics). |
|
Prefabricated
Staircases |
|
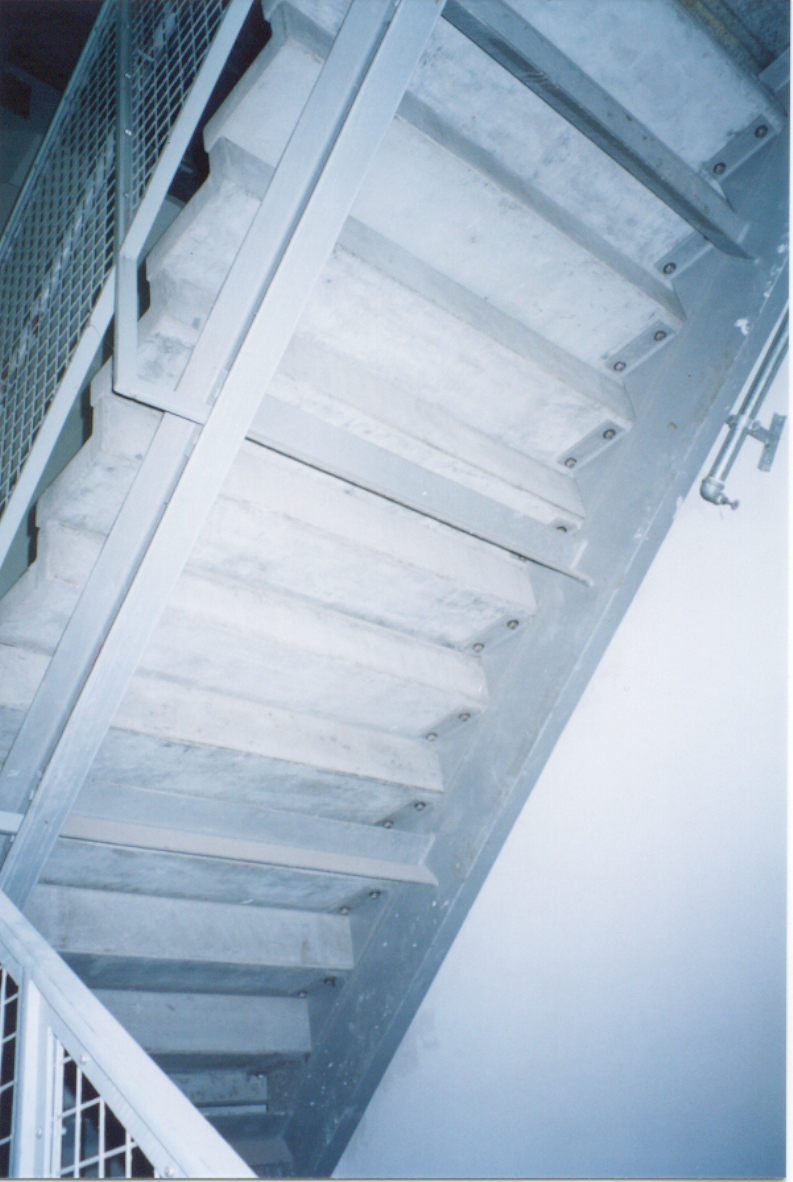 |
|
The stairs
were fabricated in, and delivered to site by sea. The prefabrication techniques
saved time, cost and ensured quality. |
|
Prefabricated
Curtain Wall |
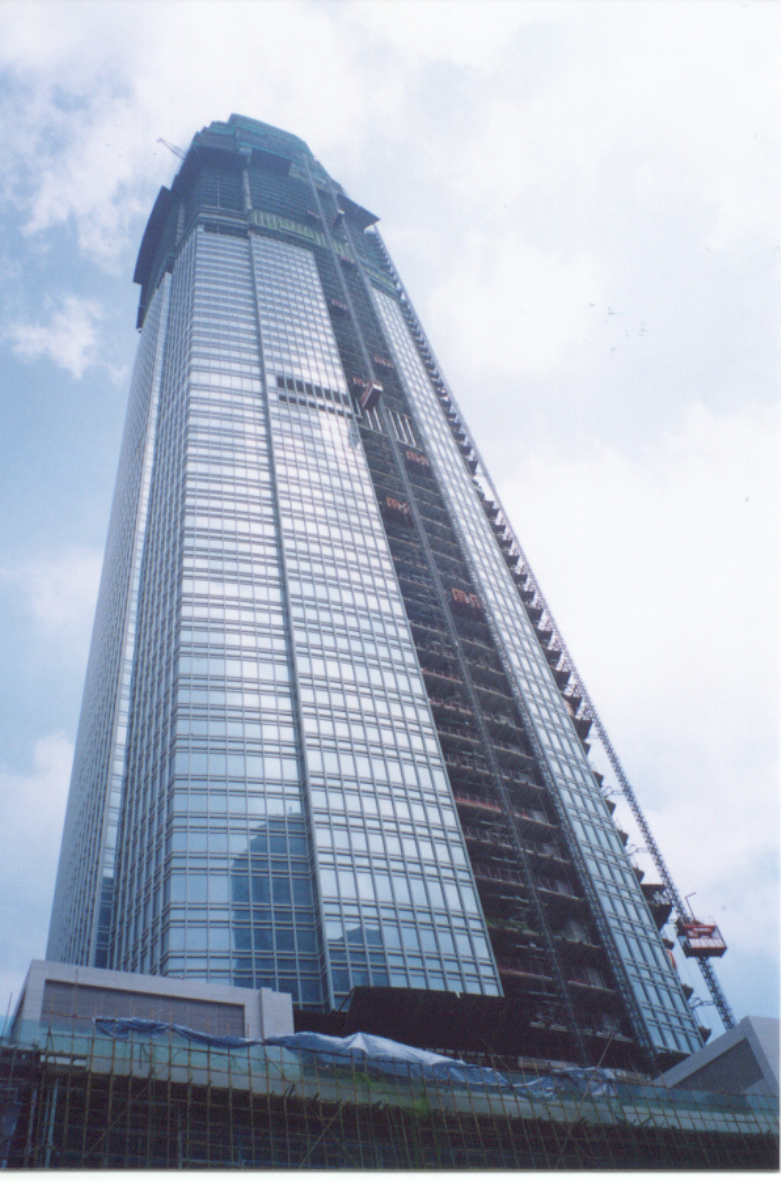 |
|
Permasteelisa is
responsible for the design engineering, supply, fabrication, assembly and
installation of the composite curtain wall system, glass walls and glass
canopies, glazed entrances and revolving doors at the podium levels as well as
the aluminum cladding on the roof fins at the top of the building.
The project
includes:
70,000 m2 of curtain wall,
6,000 m2 of glass wall,
3,000 m2 of suspended glass canopies,
2,000 m2 of glass louvers,
5,000 m2 of aluminum cladding for roof fins.
The design of the façade is based on the concept of a “pilaster” unitized panel
system where the units are prefabricated off-site and delivered to the site on
pallets ready for installation. The unitized panel system comprises cast-in
anchors, aluminum or steel fixing brackets, extruded aluminum framing, double
glazed vision units or monolithic glazed spandrel units with GMS shadowbox,
glass louvers, exterior mounted aluminum and stainless steel architectural
tubes. For the typical tower, the majority of the panels on Level 6/7 to 88 are
designed based on the vertical curtain wall system, hanging from floor to floor
4,170 high by approximately 1,610 wide for office floors and 4,850 by 1,610 for
trading floors. |
|
Retail Bridges |
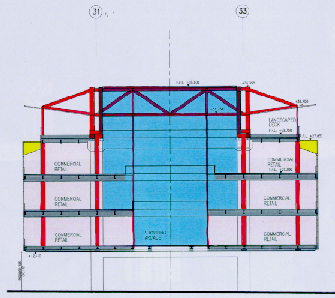 |
|
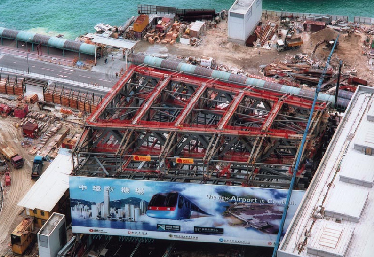 |
|
The steel
structure of the retail bridges was prefabricated in Southern China and
delivered to the site by sea. Bridges were erected within three months before
road openings. |
 |
Construction Materials |
 |
Excavated Materials : 1,000,000 m3 |
 |
Concrete : 500,000 m3 |
 |
Reinforcement : 100,000 tonnes |
 |
Structural Steel : 38,000 tonnes |
|
Waste
Management |
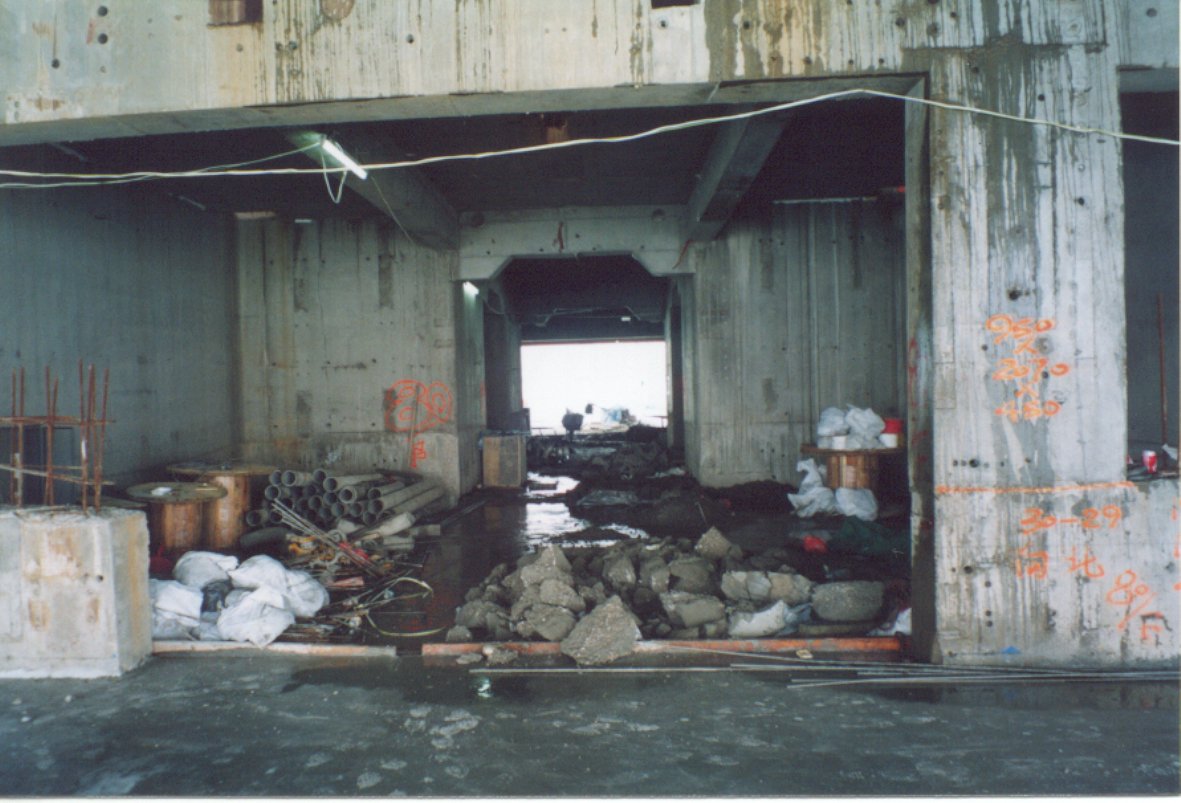 |
|
The excavated
waste arising from the construction of the 6-storey basement, was transported by
barges to the Disney reclamation site in Lantau Island. |
|
Waste arising
from construction (mainly packaging, concrete and timber) which was about 6
trucks a day were transported to landfills. The amount of waste generated
on-site was reduced by the use of prefabrication techniques. |
 |
|
Contact of Contractor |
E Man-Sanfield
JV Construction Co. Ltd. |
|
 |
|
3D Animations |
|
 |
jack-up and
jumpform. |
|
Take a
look of jack-up movie |
Take a
look of jumpform movie |
 |
|
|
|